incinerator plants
Download
Click below to download our catalogue
DWA has fabricated and supplied 2 Incinerator plants, 100kg/h, running 24 hour per day, for solid & liquid waste treatment in Lorestan & Mahabad petrochemical plants in Iran. All EPC has been conducted completely by DWA.
DWA Incinerator plant is based on cost effective, less investment of equipment ,and resource circulation plant. The plant is consisted of drum lifters, belt & screw conveyors, crusher or shredder systems, automatic feeding system, rotary kiln, post combustion chamber, lncoloy hot gas inlet tube, lncoloy quencher, bag filter, wet scrubber, induced draft air fan, stack, forced draft combustion air fan, NaoH chemical tank, liquid waste storage tank, water circulation tank, pumps, valves, electric & instrument systems, PLC automatic control system. According to hazardous classification by customer, explosion proof motors with auxiliary equipment are applied. Either fuel gas or diesel fuel is applied. All flue gas is met to international emission standards. Fabrication, test & inspection procedures is also followed to international standard. This plant can be applied to MSW and Medical waste treatment.
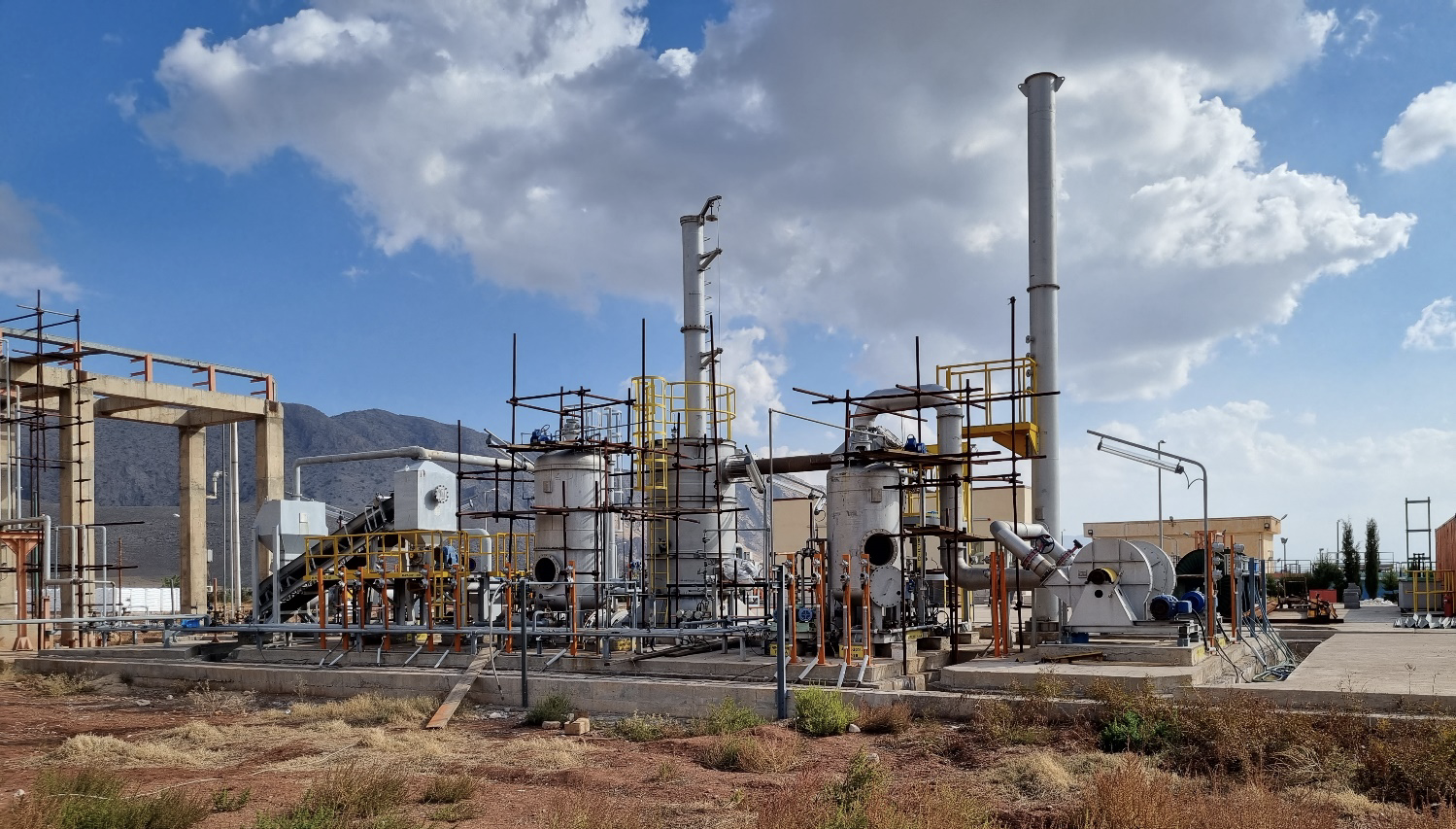
Post combustion furnace connected to Rotary Kiln
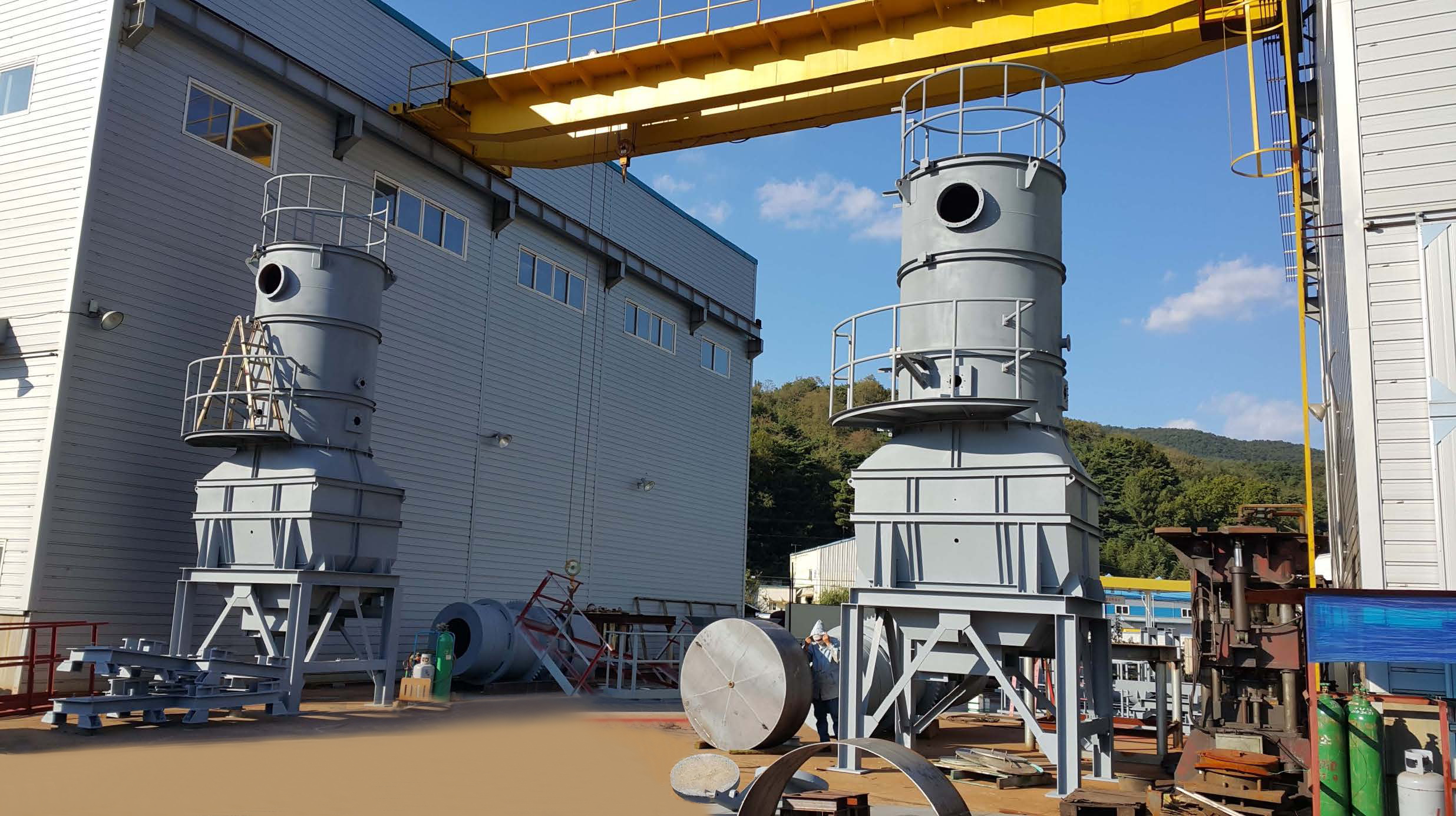
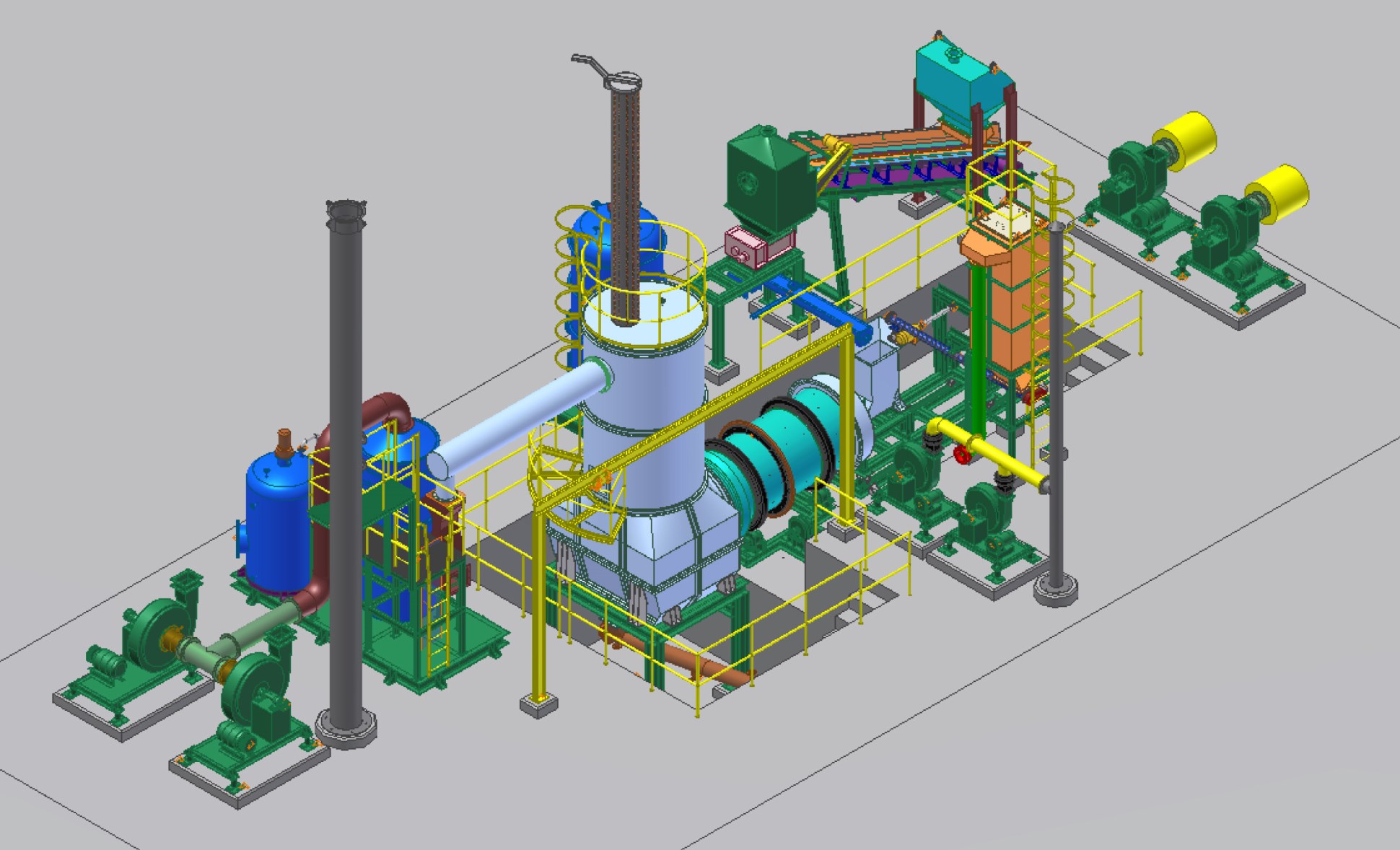
Post combustion furnace connected to Rotary Kiln
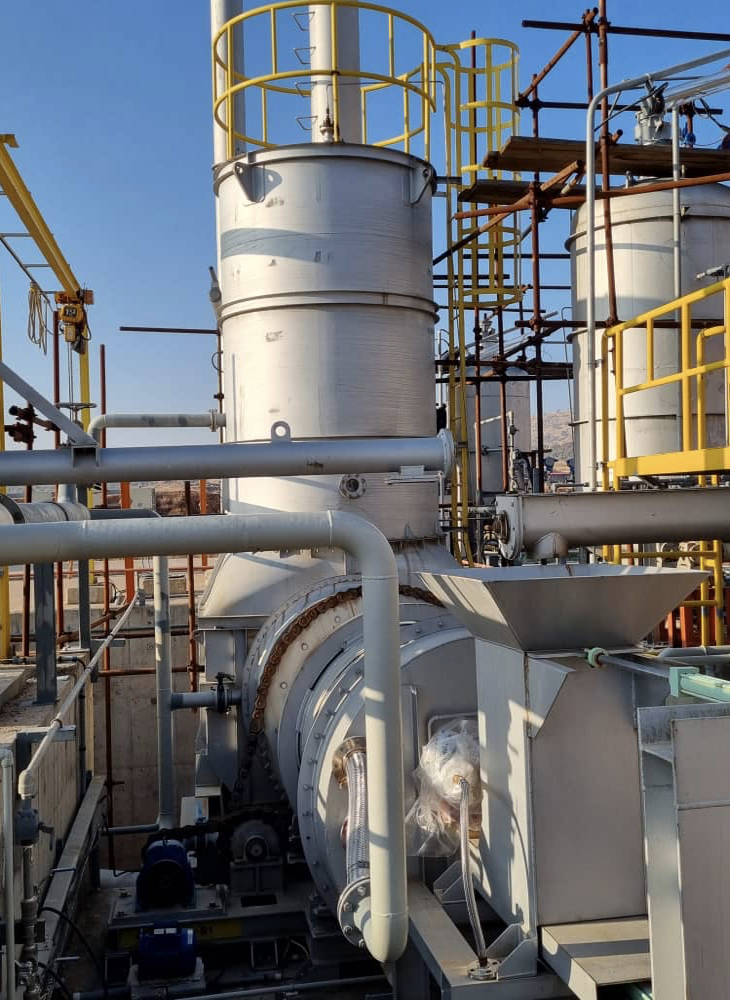
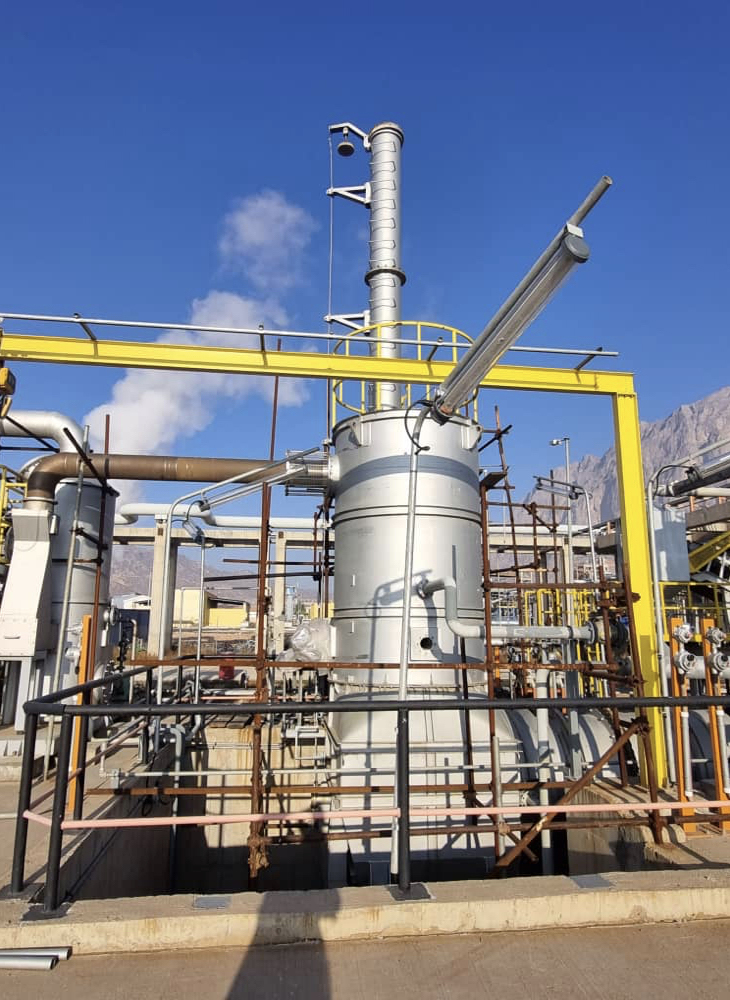
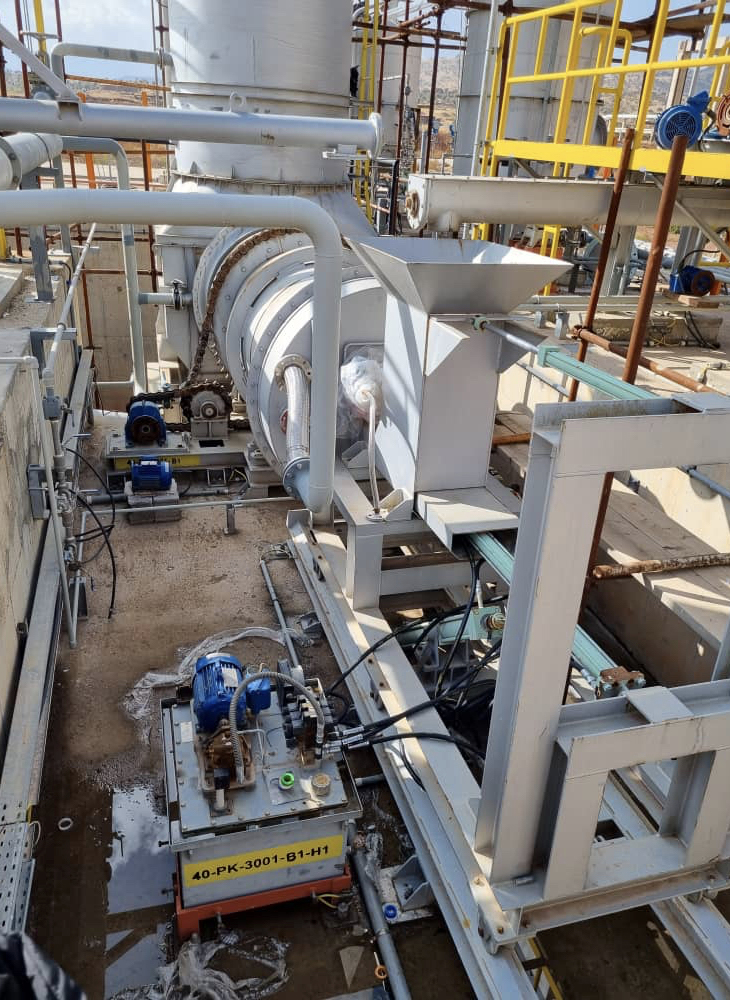
Installation photos for Rotary Kiln, Post combustion chamber, Automatic waste feeding system and others.
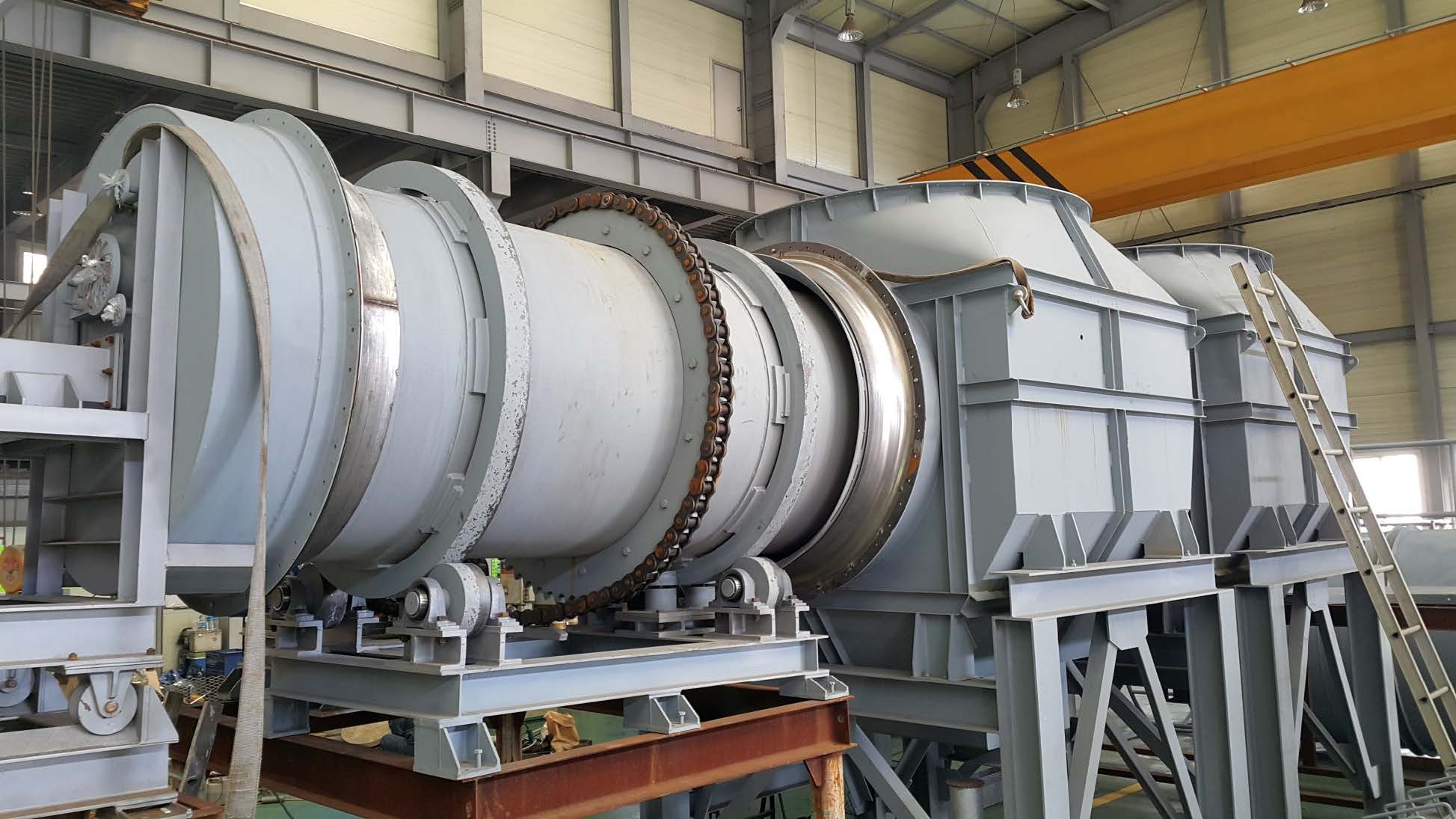
Rotary kiln is the solution for complete combustion of solid & liquid waste without accumulation of waste inside offurnace. Rotation speed of rotary kiln is 1.Sm/min. Inside of rotary kiln will be layered by castable refractory, which is resistant to 1,600°c.
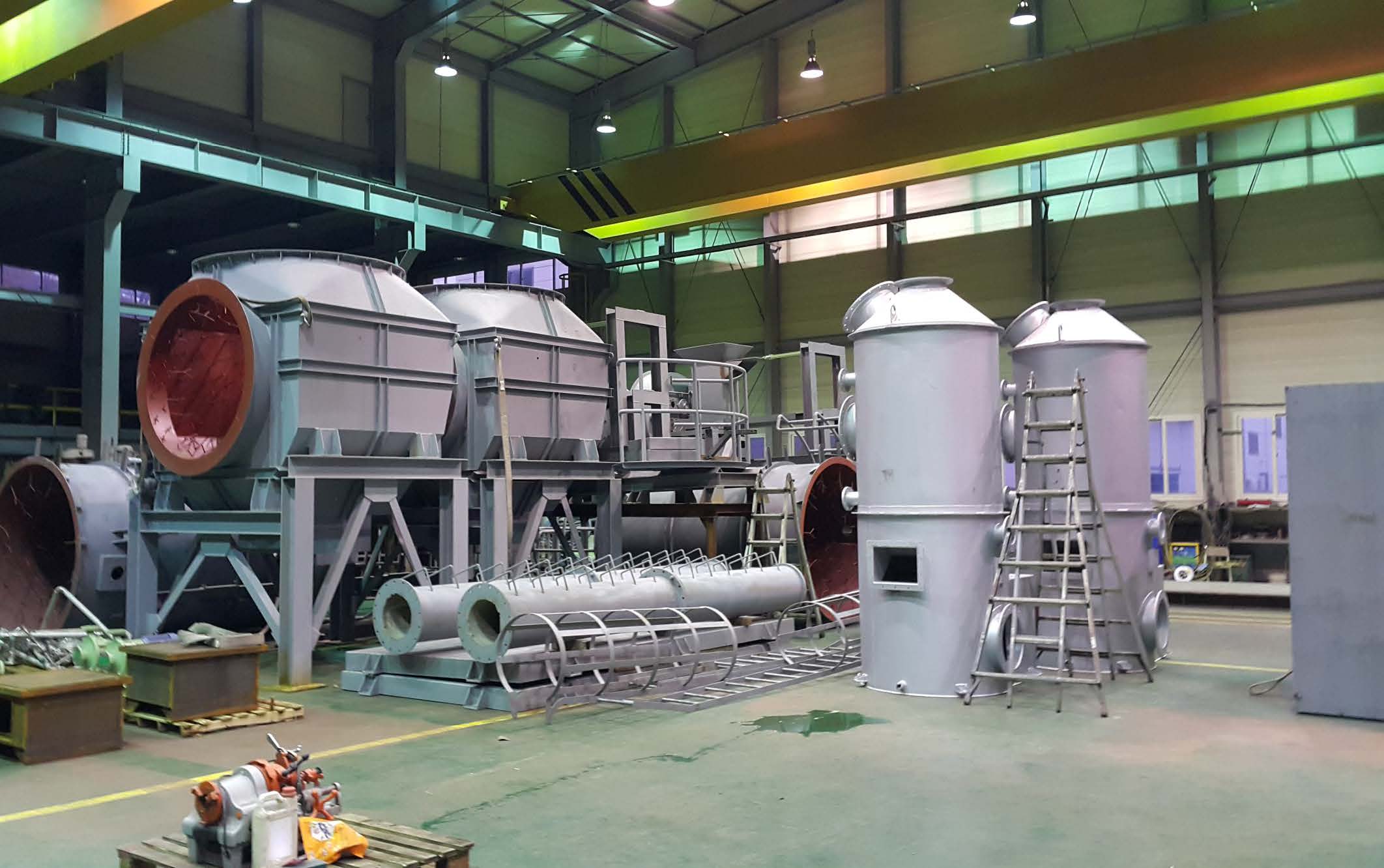
Fabrication pictures for plant. Lower parts for post combustion chambers which are connected to Rotary Kiln, Emergency stacks, wet scrubbers, automatic waste feeding systems.
Induced and Forced air fans. Hydraulic power units for the run of automatic waste feeding system.

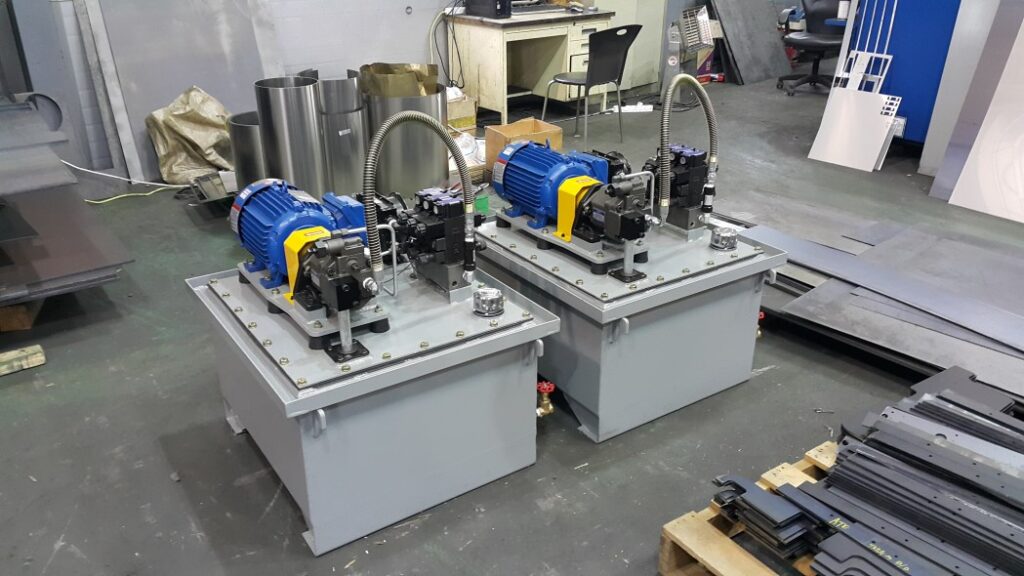
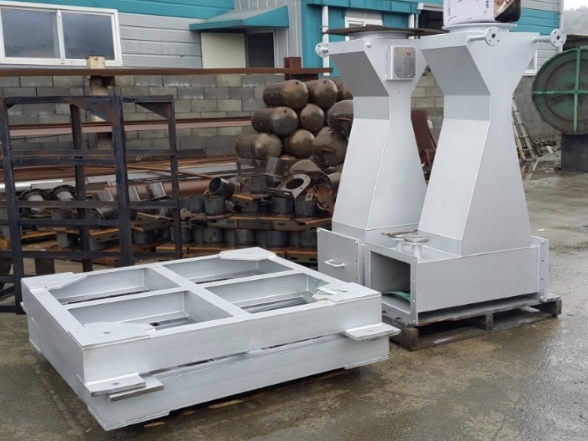
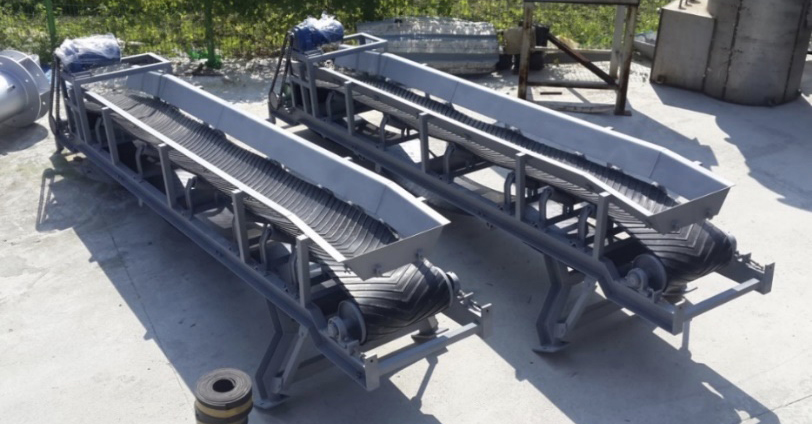
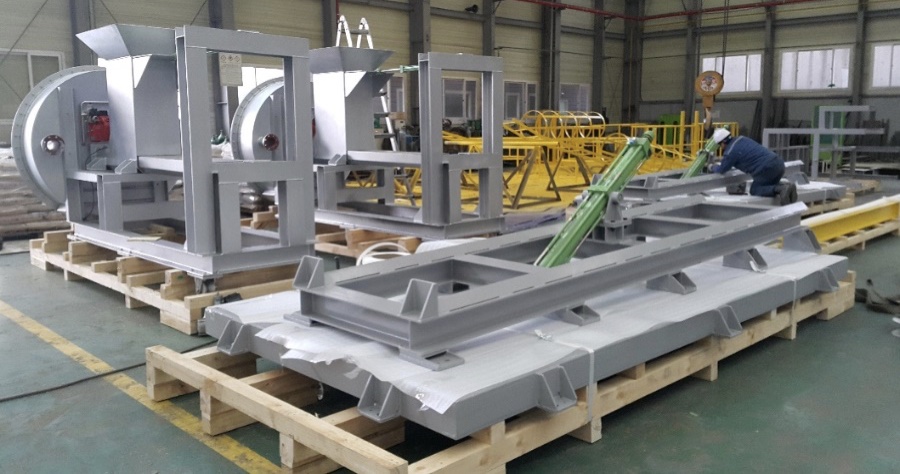
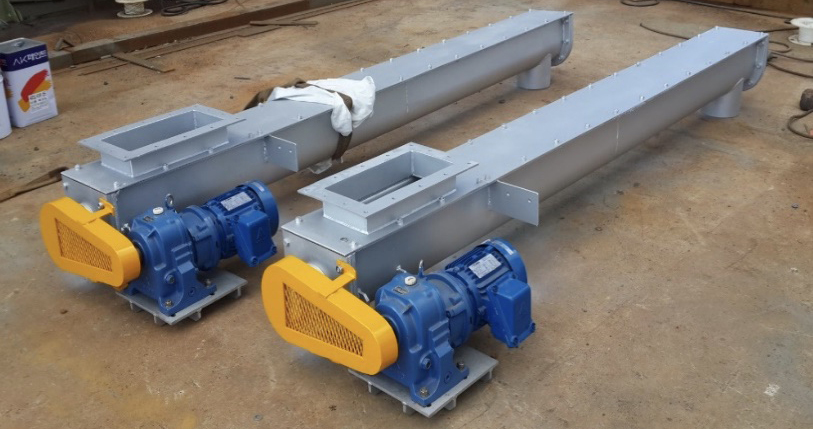
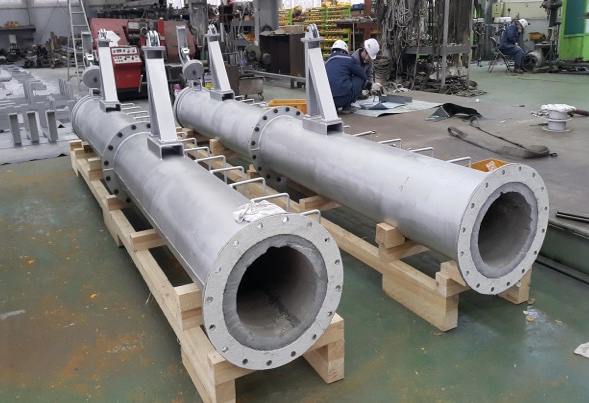
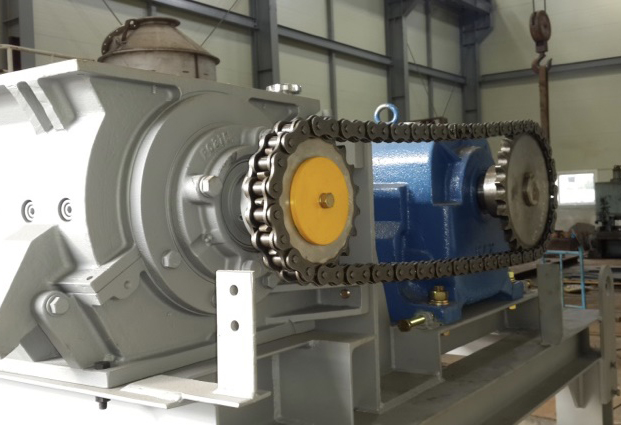
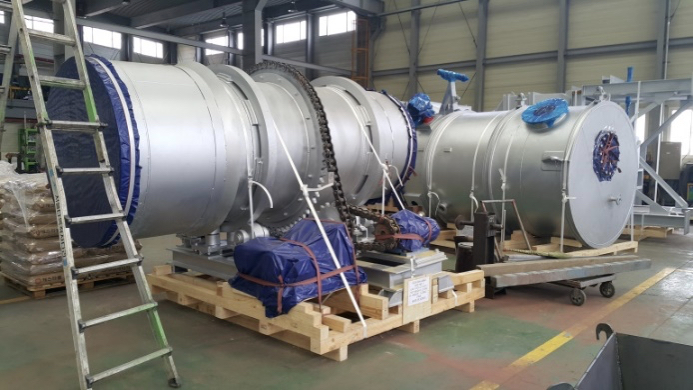
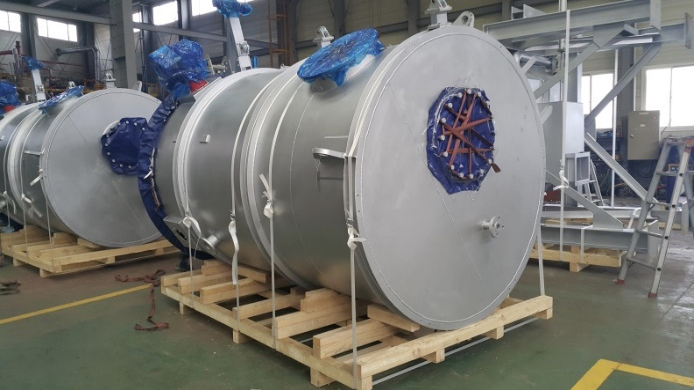
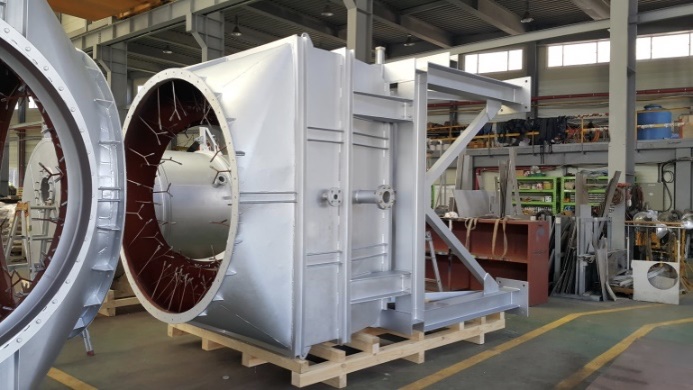
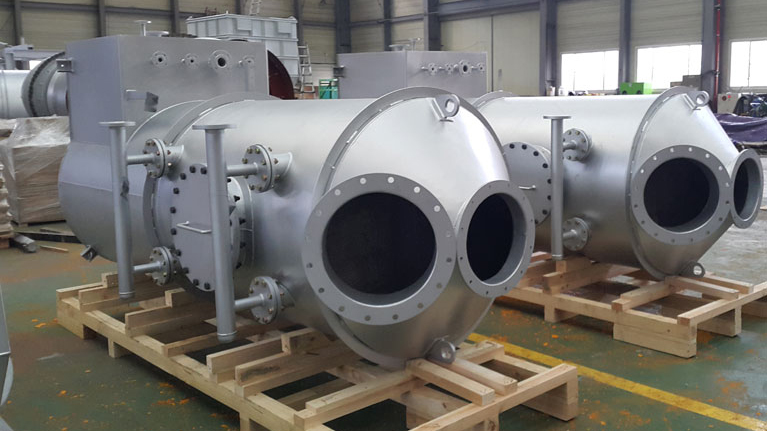
Gas burner installed in Rotary Kiln.
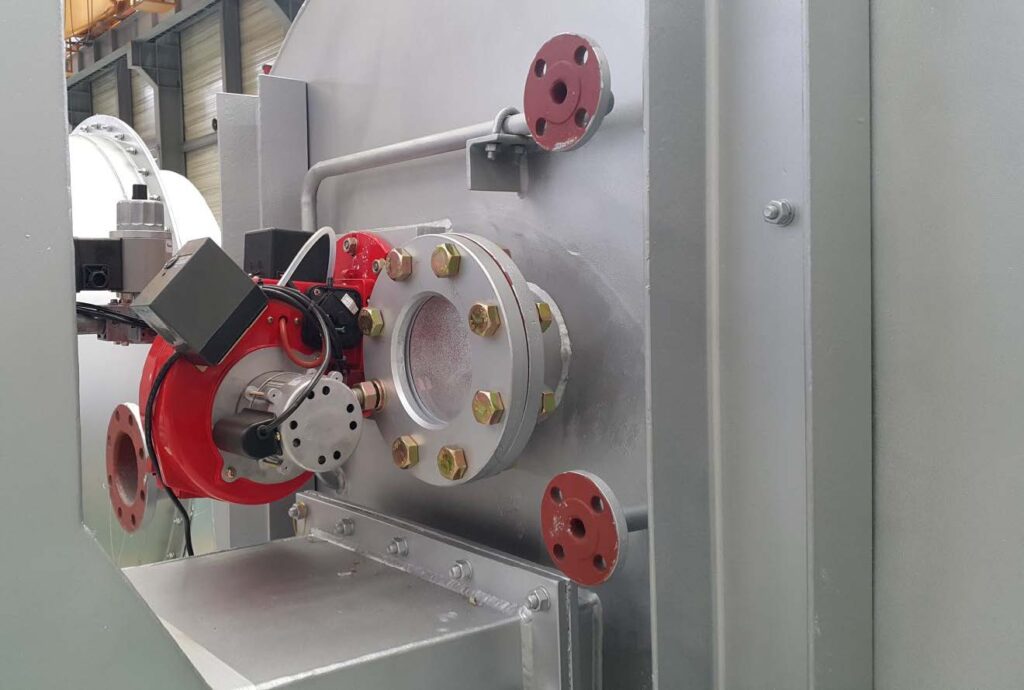
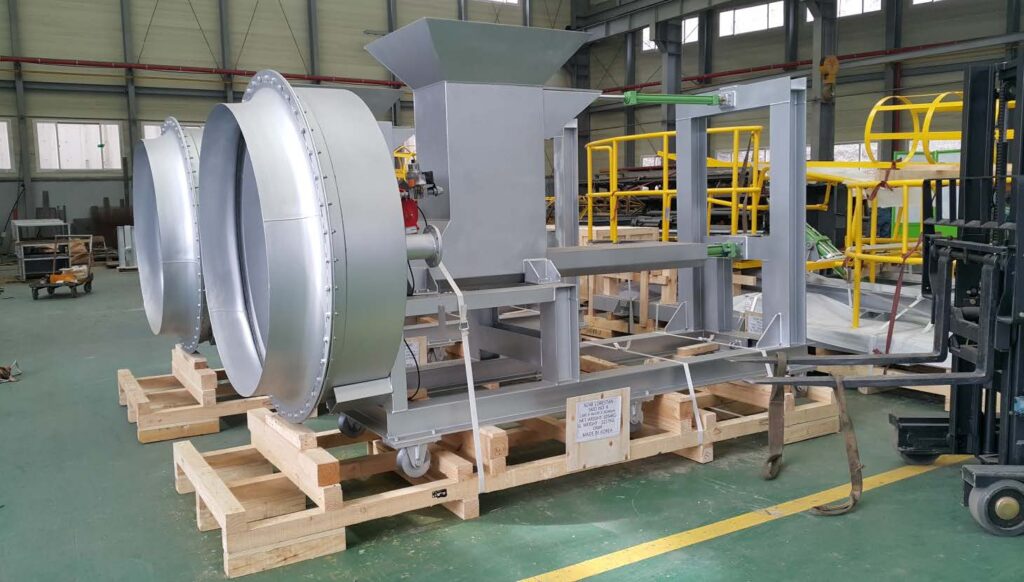
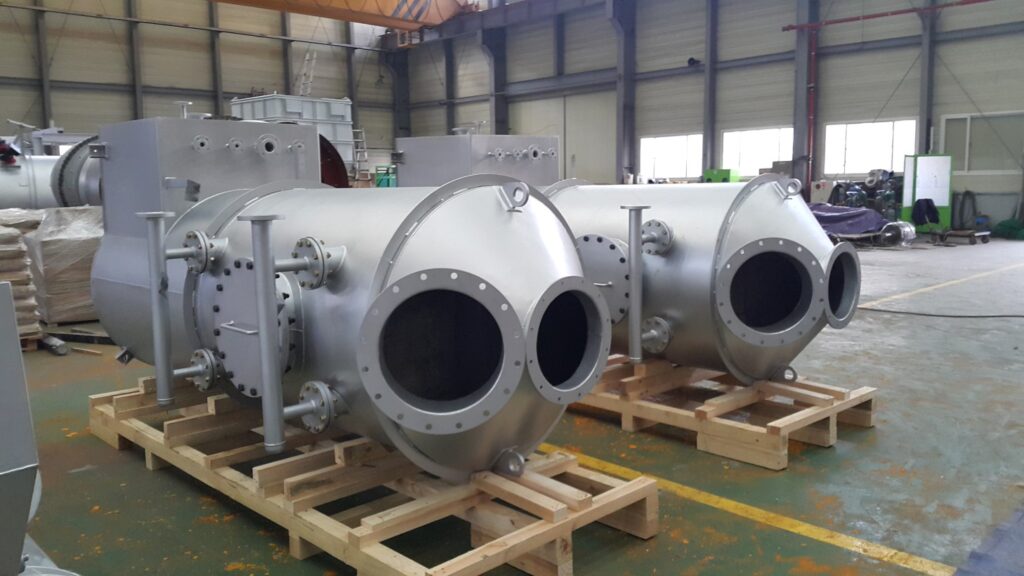
Emergency stacks installed on post combustion chamber to discharge abnormal hot gas and actuated by pneumatic cylinders.
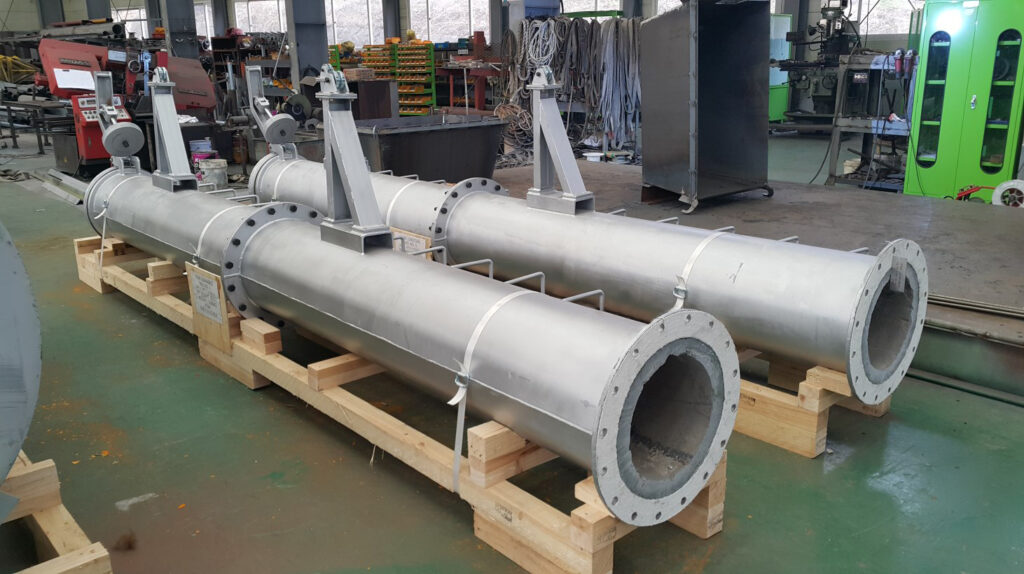
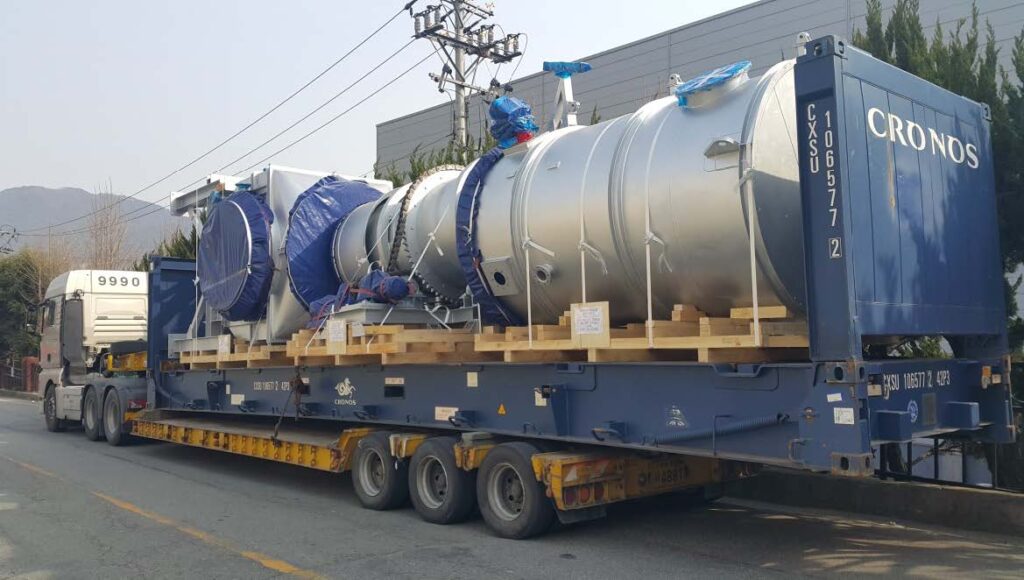
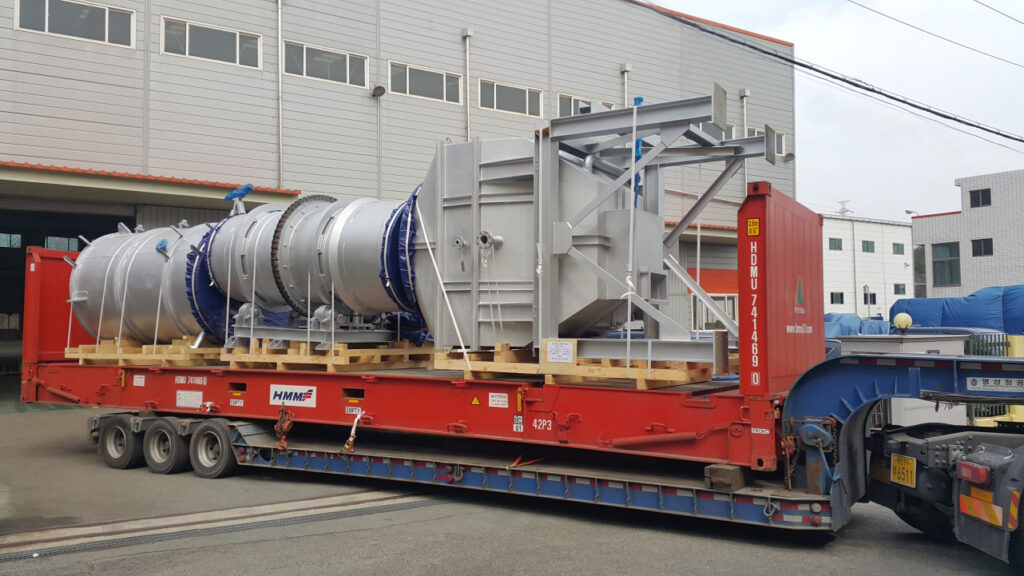
Incinerator Equipment
DWA 150, 150 to 200 kg/h of capacity. Delivered to Vladivostok Russia
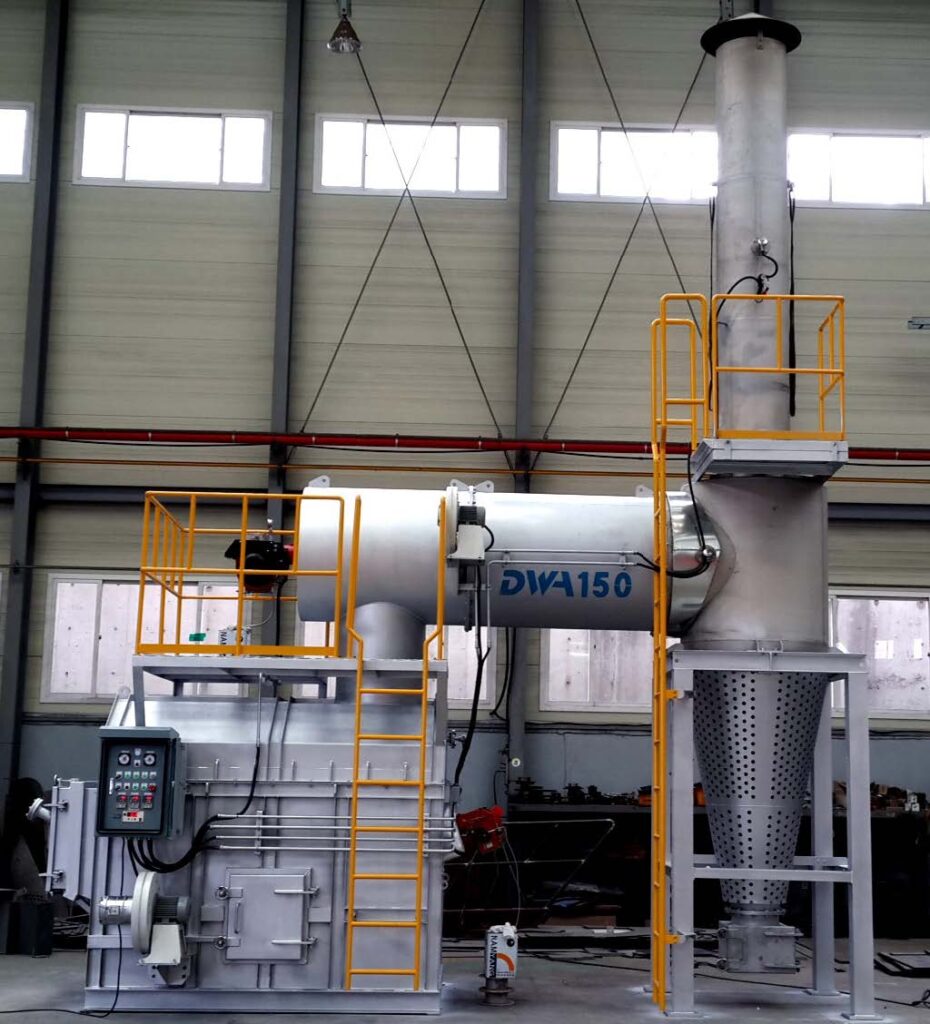
DWA fabricates and supplies Incinerator Equipment for municipal solid waste, petrochemical solid and liquid wastes, medical waste, sewer sludge, and industrial wastes. DWA’s Incinerators series are consisted of waste input door, 1st & 2nd combustion chambers, 1st & 2nd cyclones, ash discharge doors, dust box, 1st burner (On/Off), 2nd burner fuel controlled automatically, 1st & 2nd air fans, and PLC operation panel. Combustion and flue gas temperature is indicated on control panel. Combustion temperature in 2nd combustion chamber is controlled automatically according to set temperature on control panel. Air fans and 1st and 2nd combustion burner are interactive by programmned logic circuit. Combustion temperature is controlled and adjusted Oto over 950°C. Very simple & economical operation and no maintenance is featured by DWA series.
DWA 150, 150 to 150 kg/h of capacity. Delivered to Bagdad Iraq
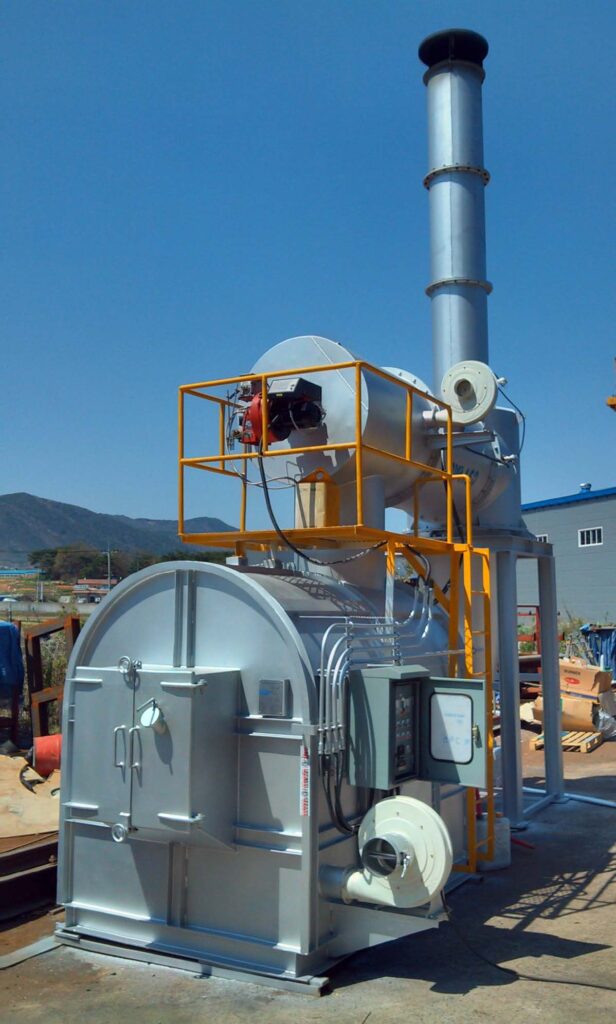
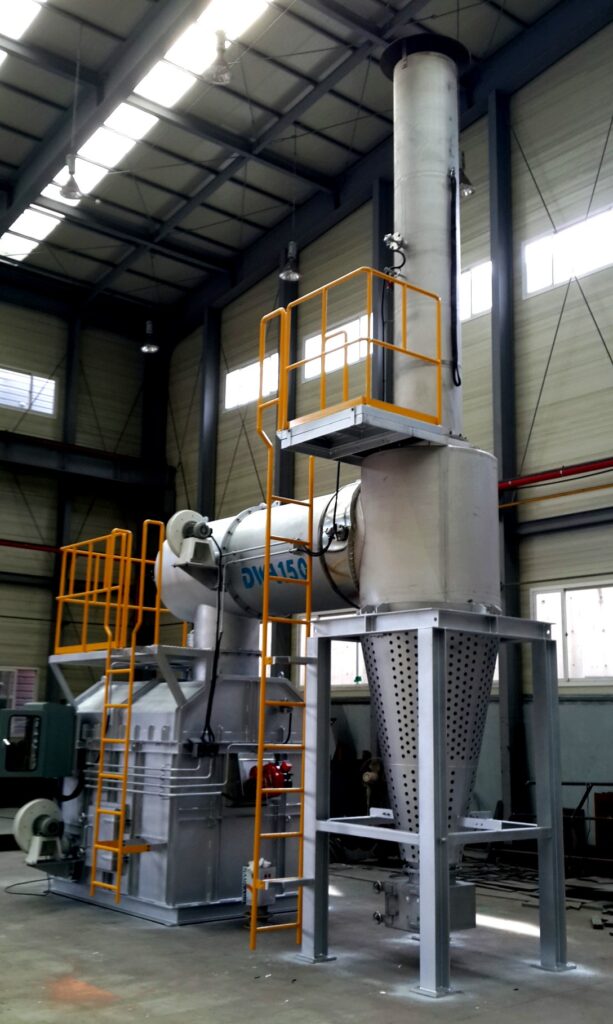
Features
- 1st combustion chamber is made of structural steel lined with Castable refractory, C401, GR. C
- 2nd combustion chamber is made of structural steel lined with Castable refractory, C401, GR. C
- Heat resistant temperature for Castable Refractories is more than 1,600°C.
- On/Off automatic operation burner for 1st combustion chamber.
- Proportional & automatic fuel controlled burner for 2nd combustion chamber.
- 1st & 2nd air blowers, and air controlled damper are installed on 2nd combustion chamber.
- Dust capturing by the scrubbing of 2 sets of cyclones and decrease flue gas temperature by 2nd centrifugal cyclone, SS304&310.
- Temperature transmitters on 1st, 2nd combustion chamber and stack.
- Very simple operation and minimum maintenance.
- So economic, cost effective, and energy saving system.
- 850 to 1250° of operation temperature.
- Temperature at 1st & 2nd combustion chamber, and stack, will be monitored at PLC panel.
- 02, Co2 monitoring at PLC is optional by customer.
- High heat resistance painting, Aluminum RAL 9006, is applied to the equipment.
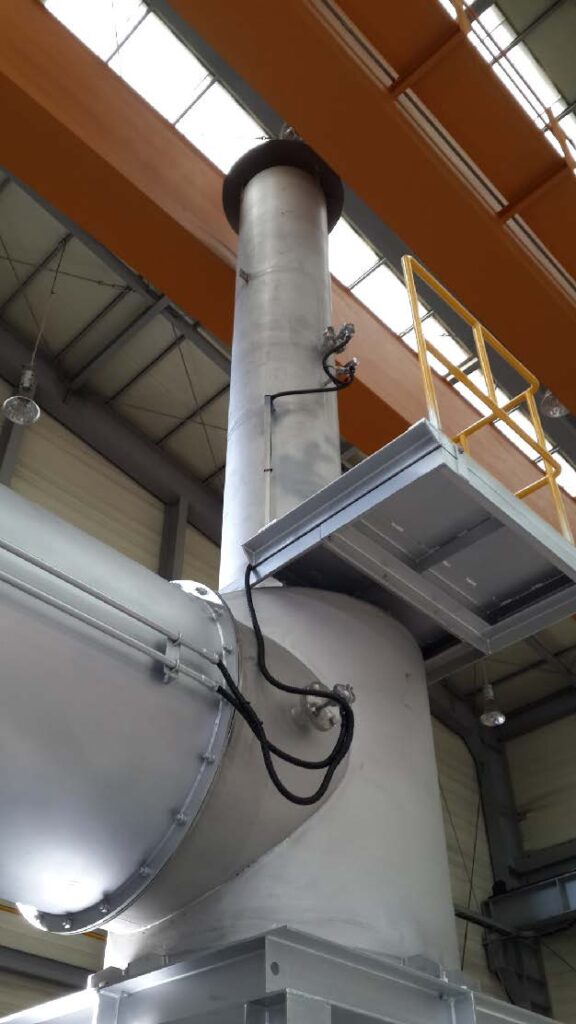
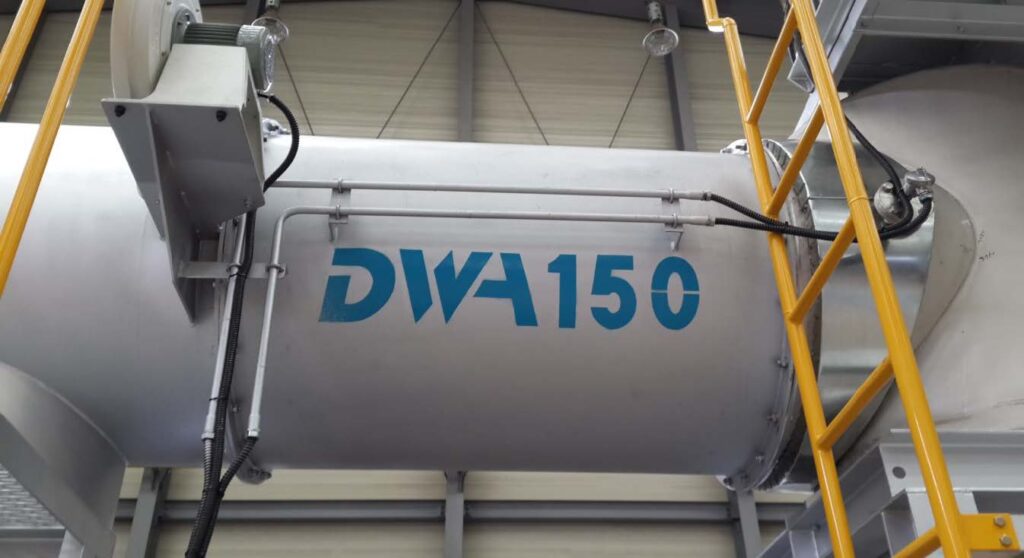
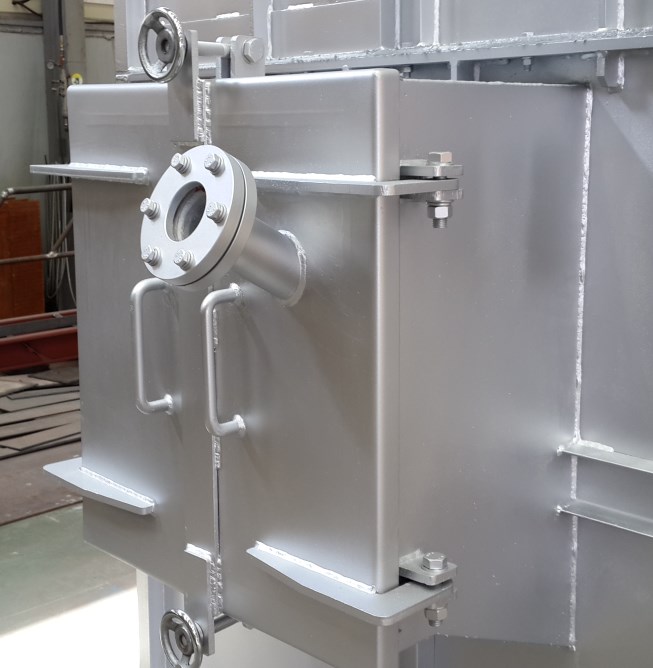
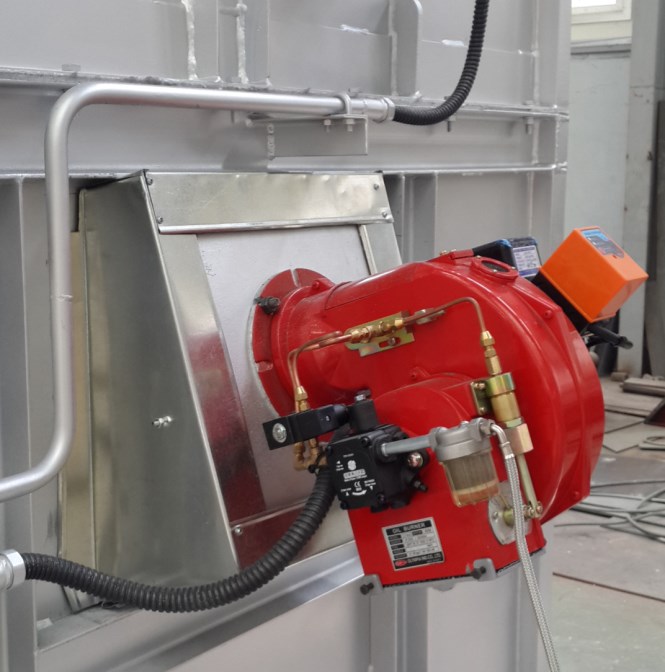
Temperature transmitters with cable trays are installed. Provide with platform, walkway, and ladder to access. Waste feeding door with a heat resistance sight glass. Automatic On/Off burner for 1st combustion chamber.1st combustion chamber burns waste. Temperature transmitter, 02, and CO2 analyzing transmitters are installed on stack. Automatic Proportional burner for 2nd combustion chamber to burn hot gas from 1st combustion chamber. High heat resistance painting, Aluminum RAL9006, is applied to coat the equipment.
Technical Information
Model | Capacity Kg/h | Electric supply kW x Hz x P | Combustion area | Dimensions W x L x Hmm |
---|---|---|---|---|
DWA100 | ~150 | 3.5 x 50 / 60 x 3 | 3.7 | 1,670 x 5,000 x 5,800 |
DWA150 | ~200 | 5.5 x 50 / 60 x 3 | 4.8 | 1,800 x 5,300 x 8,300 |
DWA200 | ~250 | 6.5 x 50 / 60 x 3 | 5.1 | 2,000 x 5,500 x 8,500 |
DWA250 | ~300 | 7.5 x 50 / 60 x 3 | 5.6 | 2,200 x 5,800 x 9,000 |
DWA300 | ~500 | 9.0 x 50 / 60 x 3 | 6 | 2,300 x 6,200 x 10,000 |